Top 10 Practical Uses For Autonomous Drones on Mine Sites
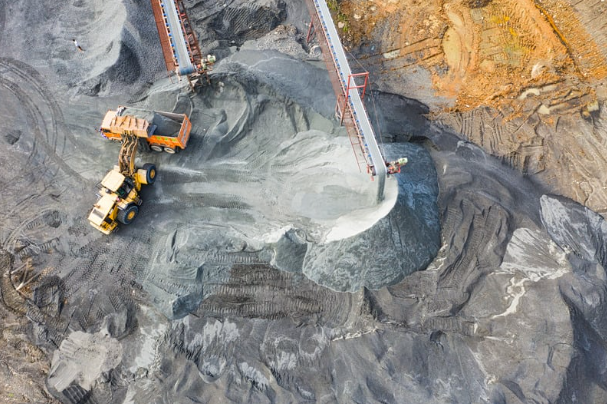
Most mines still use drones manually for basic survey work, but autonomous drones can now handle routine survey flights automatically. This frees up surveyors to focus on complex data work and gives operations teams faster access to the information they need. They can now spot issues earlier and make faster decisions using tools like 360 panoramas, thermal inspections, and on-demand remote incident response. Lots of Australian mines now use autonomous drones every day. Here are the top 10 ways they use them on site:
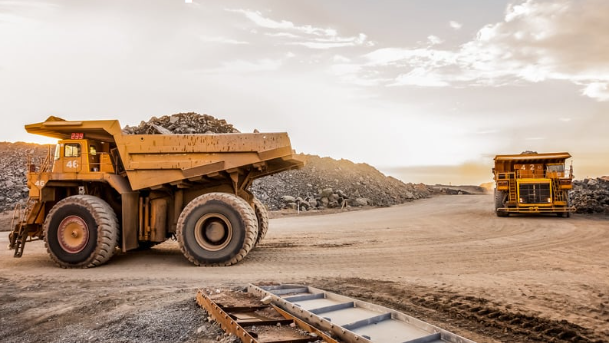
1. Autonomous haulage system obstacle clearance
When an autonomous truck stops, everything behind it stops too. On most sites, you need to send staff to physically check what’s on the road. With a DIAB system, the drone can launch and be over the truck within minutes, giving you a clear view of what’s there and whether it’s safe to move. That means faster clearance of false positives, fewer manual interventions, and better cycle times.
2. Automated stockpile surveys
Manual stockpile surveys are predictable and repetitive, but they take up hours of surveyor time. Autonomous drones can handle these flights automatically on a set schedule. Your volume calculations and 3D models are ready within hours, and automated flight patterns give you consistent image overlap and quality. Because it’s automated, you can run surveys more often: daily, weekly, or whenever you need. That means better data for planning and fewer surprises at end of month.
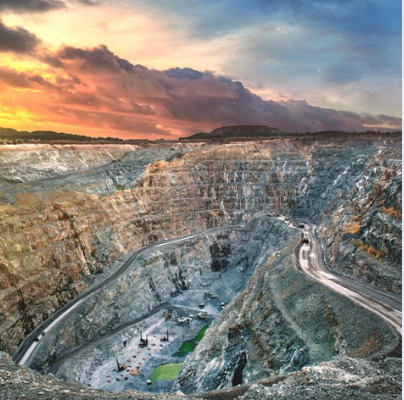
3. 360° panoramic situational awareness
It’s easier to plan when everyone can see exactly what’s happening on site. A scheduled 360° drone panorama each morning gives people a shared view of the pit: where equipment is, what’s changed over night, or if weather has affected conditions. Operational managers, engineers, and supervisors can all check the same image before work starts, without needing to walk the pit. It gives everyone a clearer picture of what’s happening on the mine, so they can plan and operate with more confidence.
4. Post-blast inspection and clearance
After a blast, it usually takes hours to get data back to the people who need it. Surveyors have to enter the pit, manually fly the drone, return to the office, then upload and process the imagery before engineers and geologists can use it. With a drone-in-a-box system, that whole process starts automatically as soon as the blasting is finished. You get essential data like fragmentation images, misfire checks, and clearance visuals quickly. No more production delays or crews waiting on standby.
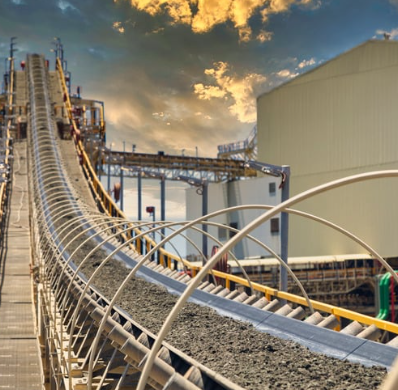
5. Conveyor idler inspection
To inspect conveyors manually, you have to send a crew out to walk the belt and it’s easy for them to miss things. Instead, you can now run pre-shift thermal scans with an autonomous drone. It scans thousands of idlers in a single flight to identify overheating rollers before they fail, which could damage the belt or start a fire. By logging temperature data overtime, you can predict failures and accurately plan your maintenance schedule.
6. Tailings dam compliance monitoring
Everyone’s watching tailings dams: regulators, insurers, and your exec team. Spotting subtle changes early means you can catch problems before they escalate. That’s why autonomous drones are now used to monitor tailings. They fly the same path each day, capturing high-res oblique images from consistent angles. It’s easy to spot subtle changes like damp patches, vegetation changes, or signs of seepage. Consistent drone imagery gives you a visual record to support compliance, reporting, and internal reviews.
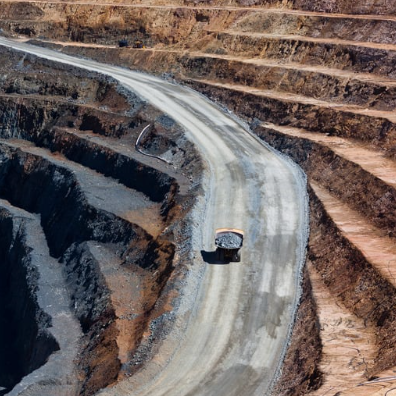
6. Geotechnical conformance and high wall scans
If pit walls move, you need to know early. But manual drone scans aren’t always done from the same angle or at the same intervals, so it’s harder to compare them and track subtle changes over time. You can now use autonomous drones to run scheduled high-res flights that capture consistent imagery of benches, slopes, and catch berms. The data integrates with your geotechnical systems, making it easy to see what’s changing to validate your stability assessments.
8. Emergency Response & Incident Management
When you face an incident like a fire, spill, or vehicle accident, the first responders are often stuck waiting. There’s no way to send anyone in until the scene is declared safe. If you launch an autonomous drone, you can get eyes on the situation fast and assess what’s happening in real-time. Then you can coordinate the right response quickly, without guesswork. Thermal cameras can also help spot heat, spills, or other risks before your team gets on the ground.
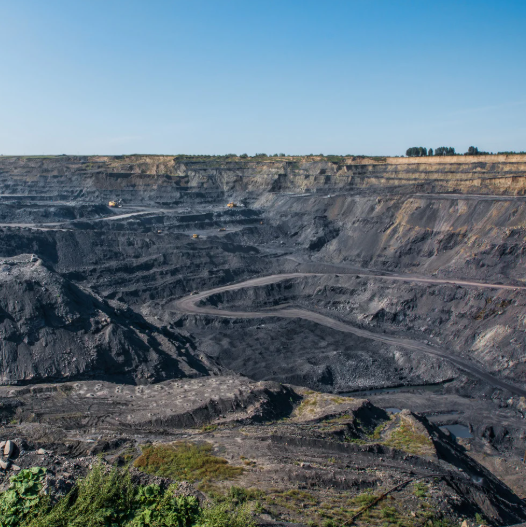
9. Burning coal and hotspot detection
Hotspots in coal stockpiles can smoulder long before there’s any smoke. If you miss the early signs, you risk fires, rework, and environmental issues. Autonomous drones can scan your stockpiles on a set schedule using thermal sensors and fixed flight paths. They pick up gradual temperature changes and flag abnormal heat before anything ignites. You get earlier warnings and can respond fast to avoid a serious incident.
10. Pipeline leak detection
On most mines, pipeline monitoring requires people to drive the length of the pipeline looking for signs of leaks. It’s slow, expensive, and small issues can easily be missed. A drone-in-a-box system can fly the same path on schedule, using AI to detect changes like pooling water, wet ground, or discolouration. The system builds up baseline imagery of normal conditions, so even subtle anomalies stand out. When an issue is spotted, you get a GPS-tagged location so maintenance crews can go straight to the problem.
How docked drones work
Docked drone systems sit in a weatherproof unit that houses the drone and its charging and communications systems. It arrives on site pre-mounted on a skid to make installation simple. Just set it on a concrete pad, connect standard 240V power, and you’re ready to go. You can also use off-grid power options like hybrid solar, battery, and diesel.
When scheduled or triggered manually, the roof slides open, the drone takes off, flies a pre-set route, and returns to recharge. The data uploads automatically, streaming live to your team via Starlink, LTE/5G, or your site network. Starlink is included by default so there’s often no need to connect to your own network, making it easy to get a trial unit running with less IT overhead.
With existing CASA BVLOS approvals already in place for more than 140 Australian locations, you can be up and running within weeks. Docked drones are also surprisingly affordable: 5 years ago, this tech used to cost $500k per unit. Now, systems like our SurveyBot start from around $50–60k.
.jpg)
How to start using docked drones. Our easy process:
We’ve helped mines of all sizes set up autonomous drone-in-a-box systems. It’s not a massive project to get a trial unit on site and flying missions. We’ll get you up and running fast with this easy process:
1. Choose a use case that solves a real problem
Start with one clear job where a docked drone will have immediate impact like post-blast surveys or daily stockpile scans. We’ll help you define a clear outcome and come up with a plan to get you there.
2. Install the system and get flying
The docked drone arrives pre-mounted on a skid ready for us to install it and train your team. You just need a concrete pad and standard 240 V power to get started, so most sites are up and running within days. We’ll make sure you have the right approvals and help with any systems integration you may need.
3. Capture and deliver data automatically
The drone flies a pre-set route, captures high-res imagery and data, then uploads it automatically when it lands. Your team gets the data fast, in the format you need, delivered straight to your existing software like Maximo and Deswik.
4. Scale up when you’re ready
Once your first use case is delivering value, you can add new missions, enable AI analytics, or expand to multiple units. Most mines automate multiple use-cases once they see what they can do with docked drones. We support you the whole time with advice, system improvements, and on-demand pilots from our remote operations centres.